
Homepage ❯ Composites ❯ Materials ❯ Here
Reinforcement
The properties of composites are dependent on the type, amount, and orientation of reinforcements that are selected for a particular service. Many materials are capable of reinforcing polymers. Although most commercial reinforcements are man-made, naturally occurring materials find use such as biomass.
There are many commercially available reinforcement materials and forms to meet the design requirements of the user. The ability to engineer the reinforcement architecture allows for the optimized performance of a product that translates to weight and cost savings.
Today, glass fibers account for more than 90% of the fibers used in reinforced polymers because they are inexpensive and have relatively good strength-to weight characteristics.

Fibers
Reinforcements = Fibers
The majority of composites are manufactured with fibrous reinforcements due to their unique features:
Fibers have high mass-specific strength and stiffness as compared to bulk materials.
Textiles can be oriented to provide tailored properties in any direction.
Fiber reinforcements carry the load efficiently along the length of the fiber to provide strength and stiffness.
Main forms of fibrous reinforcement structures:
Rovings
Mats
Woven, Stitched, Braided & 3-D Fabrics
Unidirectional tapes, tows
Prepregs
Chopped & Milled Short Fibers
Glass Fiber
Highly Versatile
Low cost
Impact resistance
Stronger than steel in certain forms
Transparent to radio signal
Electrically insulating
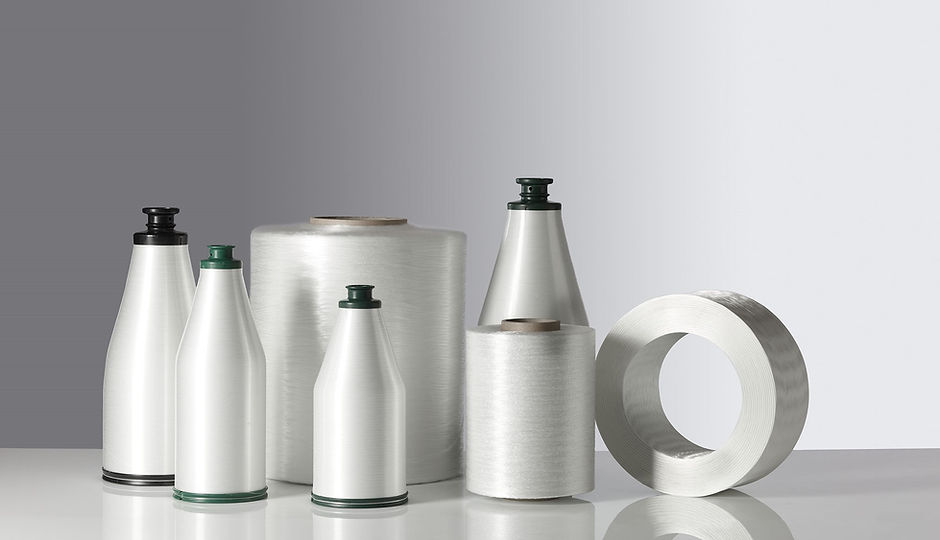
Carbon Fiber
Lightweight, Strong
High temperatures
High strength
High modulus
Extremely lightweight

High-Performance Polymer Fibers
Extremely Tough, Lightweight
Aramids, UHMWPE, LCPs etc.
Low density
Damage / impact resistance
Compression
Flexible
Heat, electricity insulation
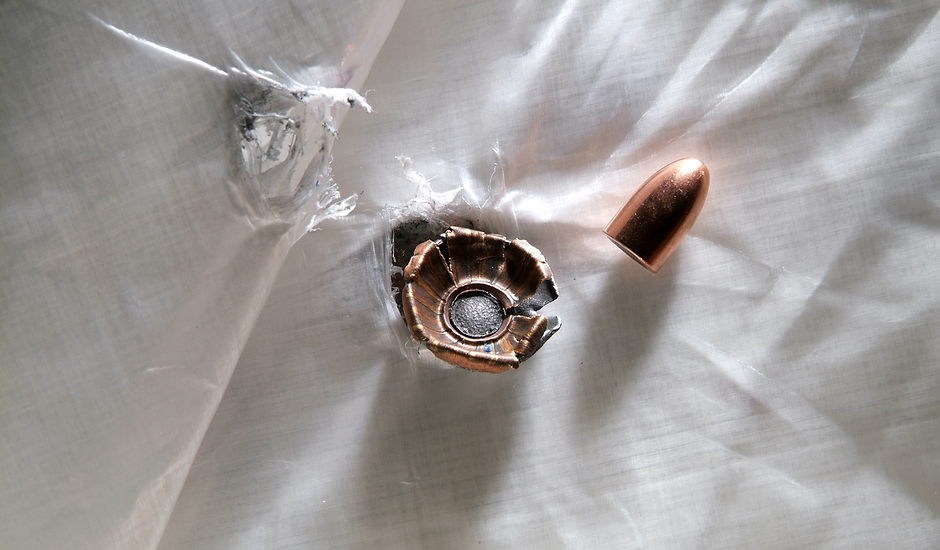
Additives & Fillers
Design Flexibility
Additives are used in composites to modify materials’ properties and tailor the laminate’s performance. When added to the resin, fillers can reduce cost and improve properties including water resistance, weathering, surface smoothness, stiffness, conductivity, and stability.
Common fillers: calcium carbonate, kaolin, clays
Fumed silica
Fire retardants
Hollow glass beads
Conductive additives
